Role of Digital Twin In the Manufacturing Industry
Digital twin:-
Digital twin in manufacturing industry can provide a real-time, dynamic view of the manufacturing process, and can be used to identify potential problems and optimize performance. For example, if a machine in a factory is starting to show signs of wear, the digital twin can be used to predict how long the machine will last and what kind of maintenance will be needed. This information can then be used to plan for downtime and improve the overall efficiency of the manufacturing process. Digital twin technology is still in its early stages, but it has the potential to revolutionize the way manufacturing is done.
Digital Twin In the Manufacturing Industry
Digital twin in manufacturing industry are becoming increasingly popular as a way to manage data and improve efficiency. They are a digital representation of a physical product or process, and can be used to monitor, control, and optimize that product or process. Digital twins can also be used to predict maintenance needs and schedule downtime for maintenance. By understanding how a production line is performing, manufacturing companies can make adjustments to improve efficiency and productivity.
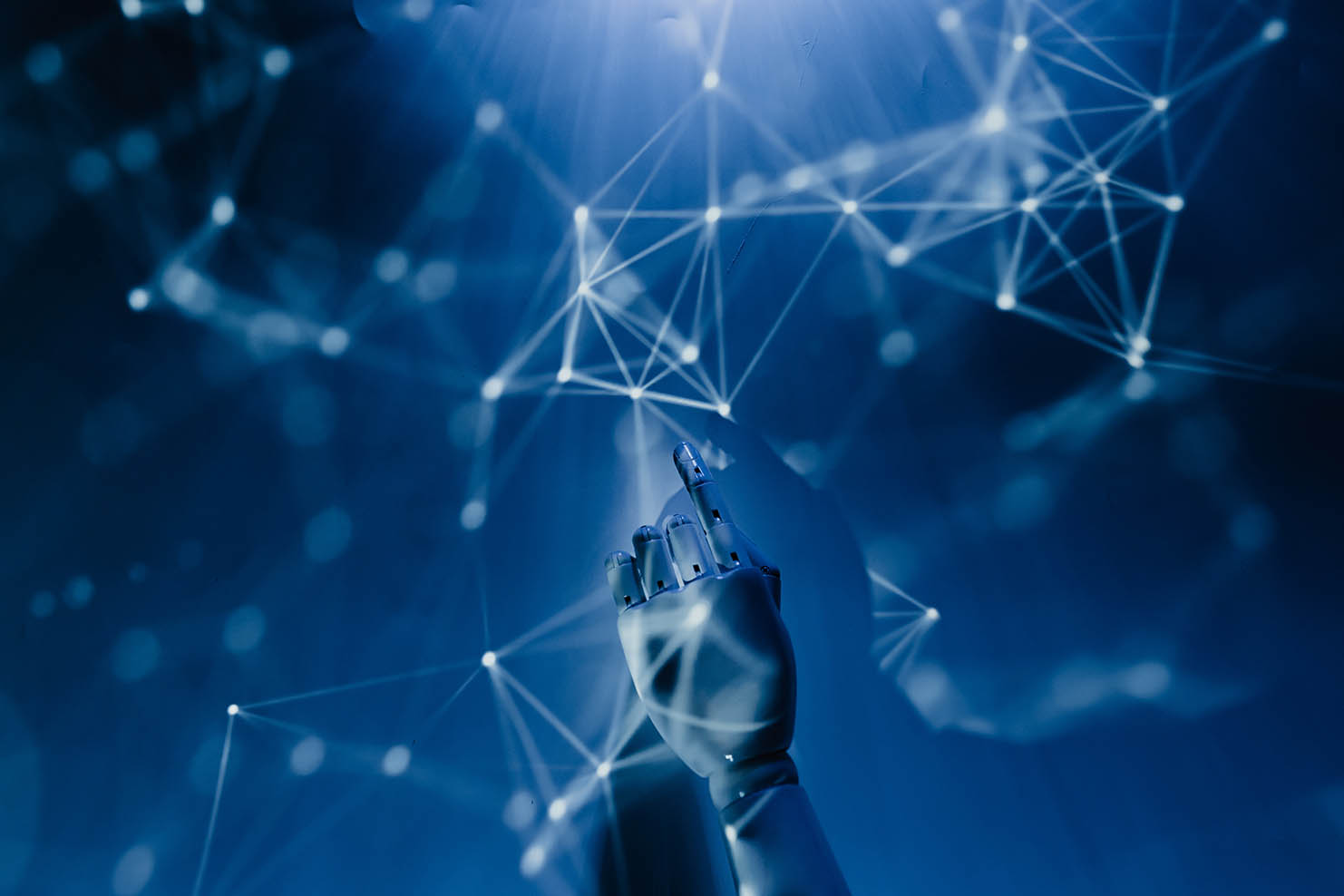
What is a digital twin?
Digital twins are created by collecting data from sensors and other sources. This data is used to create a digital model of the object or system. The digital model is then used to simulate the behavior of the physical object or system.
Digital twins are often used in manufacturing. They can be used to predict the behavior of machines and other manufacturing equipment. This can help manufacturers improve efficiency and avoid downtime.
Digital twins can also be used in other industries, such as healthcare and transportation.
A digital twin in manufacturing is an exact, real-time replica of a physical product, system, or process. It captures data from every stage of the manufacturing process, allowing manufacturers to identify inefficiencies, optimize performance and predict problems before they happen.
Digital twins are changing the way manufacturers do business, and the potential benefits are huge. By reducing downtime, waste, and costs, digital twins can help manufacturers increase productivity, efficiency, and quality, while also improving safety and reducing environmental impact.
A digital twin is a digital replica of a physical object that can be used to track, monitor, and simulate real-world conditions.
A digital twin is a digital replica of a physical object or system. In manufacturing, a digital twin can be used to track the performance of a production line or individual piece of equipment in real-time. This information can be used to improve efficiency and quality control.
What Is a Digital Twin in Manufacturing?
In the simplest terms, a digital twin in manufacturing is a digital representation of a physical object. Often, this is used to indicate how well a product is performing, or how an assembly line is working. Additionally, it can be used to diagnose problems virtually, without having to take the physical product apart.
Digital twins are created by pairing data from sensors with computer models. This data can come from a variety of sources, including RFID tags, GPS systems, and accelerometers. Once this
Digital twins in manufacturing industry help improve productivity by providing accurate, real-time data about machines and processes. By understanding how machines and processes are performing, manufacturers can make adjustments to improve efficiency and quality.
Digital twins can also be used to simulate different manufacturing scenarios, allowing manufacturers to plan and test changes before implementing them.
A digital twin in manufacturing is a virtual copy of an existing physical product or process. It captures data from the manufacturing process and allows manufacturers to test and optimize their processes in a virtual environment before implementing them in the real world. This can help to improve efficiency and quality and reduce costs.
Digital twins in manufacturing are digital replicas of physical machines, products, or production lines. They are used to simulate real-world conditions and to test and optimize digital designs. Digital twins can help improve quality control, speed up production times and reduce costs.
Why is a digital twin important?
A digital twin can help improve the efficiency of the manufacturing process by identifying potential issues before they occur. By simulating the manufacturing process, a digital twin can help identify bottlenecks and optimize the process. A digital twin is a digital replica of a physical object or system. It can be used to simulate and predict the real-world behavior of its counterpart.
A digital twin in manufacturing is a digital replica of a physical product or production line. It can be used to simulate how the product or production line will operate under different conditions, optimize performance, and predict problems before they occur.
A digital twin in manufacturing is a digital replica of a physical object or system. In manufacturing, a digital twin can be used to simulate the manufacturing process and identify potential issues before they occur.
Manufacturing Digital Twin:-
- A digital twin in manufacturing can help improve production processes and quality control.
- A digital twin can serve as a virtual representation of a manufacturing process or product, allowing for a better understanding and analysis of that process or product.
- A digital twin in manufacturing can help reduce downtime and improve efficiency by providing real-time data and feedback on performance.
- A digital twin can help improve communication and coordination among different teams and stakeholders involved in manufacturing processes.
- A digital twin can ultimately help improve the quality and competitiveness of manufactured products.
How can a digital twin be used in manufacturing?
A digital twin can be used to simulate the manufacturing process and identify potential issues before they occur. By understanding how the manufacturing process works, a digital twin can help identify bottlenecks and optimize the process.
BENEFITS:-
- Digital twins can also be used to track the performance of manufacturing equipment and processes in real-time. This information can be used to improve productivity and efficiency.
- By using digital twins in manufacturing, companies can create a replica of their manufacturing process and equipment. This replica can be used to simulate different production scenarios and predict problems before they occur.
- Digital twins can also be used to create virtual prototypes of new products or production processes. This allows manufacturers to test and refine new designs before they are built.
- Digital twins can also be used to train new employees on manufacturing processes. By using digital twins, companies can create a safe and realistic environment for employees to practice and learn new skills.
- Digital twins can also be used to diagnose and troubleshoot problems with manufacturing equipment. By using digital twins, companies can save time and money by quickly identifying and resolving issues.
Factory Digital Twin:-
A digital twin is a digital representation of a physical object or system. In the context of a factory, a digital twin can be used to track the performance of factory equipment and processes in real-time, and identify areas for improvement.
The factory digital twin is a well-written, reader-oriented, and compelling document that provides detailed information about a factory. It includes information about the factory’s history, its products, its manufacturing process, and its current status.
The benefits of having a digital twin in your factory are numerous. With a digital twin, you can have a real-time, accurate view of your factory’s performance. This allows you to make informed decisions about where to allocate resources and how to improve efficiency. Additionally, a digital twin can help you to troubleshoot problems and identify potential issues before they cause disruptions in production. Implementing a digital twin of your factory can be a major advantage in today’s competitive marketplace.
A digital twin can be used to:-
A digital twin is a digital representation of a physical object or system. In the context of a factory, a digital twin can be used to track the performance of factory equipment and processes in real-time, and identify areas for improvement.
Monitor factory equipment and processes in real-time·
Analyze data to identify areas for improvement·
Improve the efficiency of factory operations·
Reduce downtime and improve the quality of products.
Assuming you would like a definition of a Factory Digital Twin:-
A digital twin is a digital representation of a real-world entity or system. A factory digital twin is a digital replica of a manufacturing plant that can be used to simulate real-world conditions and predict how the plant will operate under various circumstances.
A factory digital twin can be used to improve efficiency and optimize production. By understanding how the factory operates, Bottlenecks and issues can be identified and addressed. Additionally, a digital twin can be used to test new protocols and processes before implementing them in the real world. This can help to avoid costly mistakes and disruptions to the manufacturing process.
Today, the idea of a digital twin is being applied to factories as a way to manage and optimize production. A factory digital twin is a digital representation of a physical factory and can be used to track data and performance in real time. This information can then be used to improve efficiency, identify issues, and make predictions about future production.
Looking to create a factory digital twin?
Here are some tips:-
- Keep it well-written: Your factory digital twin should be clear and concise, free of errors.
- Make it reader-oriented: Write your factory digital twin with the reader in mind. Keep your audience in mind and tailor your content accordingly.
- Keep it compelling: A factory digital twin is only as good as its content. Make sure your content is interesting and engaging, and that it offers value to the reader.
A factory digital twin can be used to:-
– Monitor data and performance in real-time
– Improve efficiency
– Identify issues
– Make predictions about future production
What is the importance of digital twin In manufacturing industry?
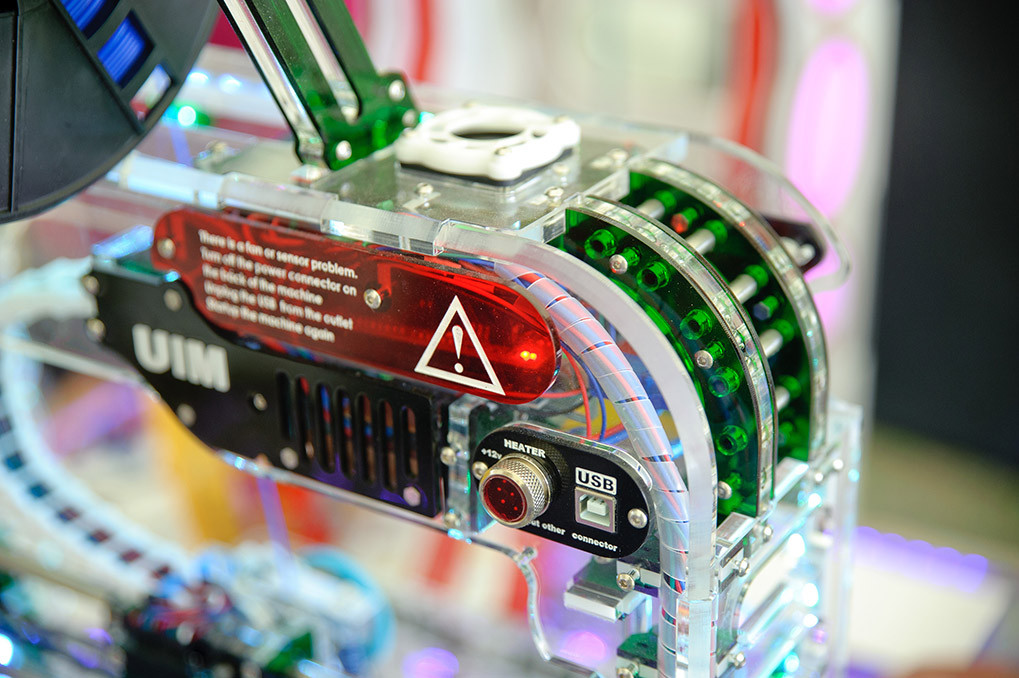
Digital twin technology is transforming the way manufacturers design, produce, and deliver their products. By creating a digital replica of a physical product or process, manufacturers can gain insights that would otherwise be unavailable, and make better decisions that improve quality and efficiency.
Digital twins can be used to track the progress of individual products through the manufacturing process, identify potential issues before they cause problems, and validate changes to the manufacturing process. By monitoring and responding to changes in the digital twin, manufacturers can make real-time adjustments to the physical process, ensuring that products are produced to the highest quality standards.
Digital twin technology is still in its early stages, but the potential benefits for manufacturers are significant. By adopting digital twins, manufacturers can stay ahead of the competition and deliver the best possible products to their customers.
- Digital twin technology is becoming increasingly popular in manufacturing as a way to replicate and optimize physical processes.
- A digital twin is a digital replica of a physical object or process that can be used to simulate and optimize that process.
- Digital twins can be used to improve the efficiency of manufacturing processes by identifying and troubleshooting issues before they cause problems in the physical world.
- Digital twins can also be used to optimize processes by investigating and testing different scenarios before implementing changes in the real world.
- Manufacturers can use digital twins to create a virtual replica of their factories, products, and processes. This allows them to test and optimize different scenarios before implementing changes in the real world.
- Digital twin technology is still in its early stages, but it has great potential to revolutionize manufacturing.
Top 10 Benefits of the digital twin in manufacturing Industry:-
- A digital twin in manufacturing can provide a real-time view of manufacturing operations, identify issues and opportunities, and help optimize performance.
- A digital twin can help managers make informed decisions about process improvements, equipment maintenance, and other areas of manufacturing operations.
- A digital twin can improve communication and collaboration between different departments and stakeholders in a manufacturing organization.
- A digital twin can provide a complete picture of manufacturing processes and performance, including data on resource consumption, quality control, and safety.
- A digital twin can help managers troubleshoot problems in manufacturing operations and identify potential areas for improvement.
- A digital twin in manufacturing can be used to create a virtual model of a manufacturing plant or process, which can be used for training and simulations.
- A digital twin can be used to create a virtual copy of a manufacturing process or system, which can be used for test and development purposes.
- A digital twin in manufacturing can be used to monitor and manage changes in a manufacturing process or system, preventing unplanned downtime and disruptions.
- A digital twin can be used to optimize and improve the efficiency of a manufacturing process or system.
- A digital twin in manufacturing can help managers to understand the impact of changes in the manufacturing process or system on the overall performance of the organization.
VERDICT:-
Digital twin technology is becoming increasingly popular in manufacturing as a way to improve performance and efficiency. A digital twin is a digital representation of a physical object or system and can be used to simulate how the object or system would operate in different scenarios. manufacturers are using digital twins to test new designs, optimize production processes, and predict maintenance needs.
Digital twins can be very useful in manufacturing. For example, they can be used to help optimize assembly lines. By understanding how a product is performing, assembly lines can be reconfigured to achieve a higher level of efficiency. Additionally, digital twins can be used to diagnose problems virtually. This can save a lot of time and money, as it can help identify the root cause of a problem without having to take the physical product apart.
Reviews